Market uptake of an automated technology for reusing old bricks
The eco-innovation of the project REBRICK demonstrates a new way for the management and reuse of demolition waste, saving energy and resources. With the new vibration-based technology it is now possible to clean bricks without using chemicals or water, improving energy efficiency and reducing environmental impacts.
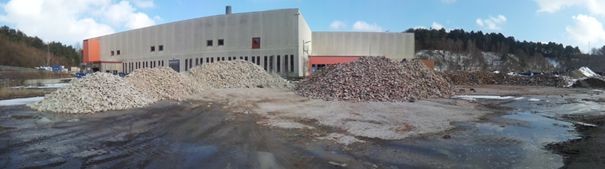
The challenge
Manufacturing of bricks requires large amounts of energy and resources. Handling demolition waste in a resourceful way, such as the cleaning and reuse of bricks, could reduce CO2 emissions as well as waste, reducing environmental impacts. Developing an automated way of cleaning bricks for reuse can significantly contribute to resource efficiency.
The innovation
The REBRICK project focused on sustainable construction through automated cleaning and recycling of clay bricks, saving 0.5 kg of CO2 emissions per reused brick, when compared with manufacturing new bricks.
The project was coordinated and managed by Gamle Mursten (Denmark) in collaboration with their partners Scan-Vibro (Denmark) and D’Appolonia S.p.A. (Italy). Scan-Vibro was responsible for technical development and D’Appolonia S.p.A. had the responsibility for market analysis as well as disseminating results.
REBRICK is a part of the Competitiveness and Innovation Framework Programme (CIP ), an initiative of the European Union, and received a public grant partial funding for demonstration from the EU.
The project aimed to develop a sustainable process for recovering recycled bricks, involving no chemical or water use, whilst ensuring high quality standards and reasonable levels of profit.
This was managed by Gamle Mursten, in cooperation with Scan-Vibro, developing a technology that uses a vibration-based system in order to handle and sort demolition waste and cleaning it without the use of either chemicals or water.
The cleaning process starts with mechanical separation of the mortar (from demolition debris from brick buildings) from other materials, such as cement and wood. Whole bricks are then separated from damaged bricks by an automated system. Whole bricks are cleaned in a (patented) vibration-based process and then sorted manually after visual inspection of characteristics, quality and color. Cleaned bricks are placed on a conveyer system, and stacked and wrapped by a robot, after which they are ready for transport to a new construction project.
In addition to developing the technology, the REBRICK project aimed to accomplish commercial scale production, customized to different European regions with different requirements in labor costs, brick weight and mortar types. Developing a comprehensive marketing strategy as well as establishing sale channels also ensured a faster introduction to the European market.
Why did it work?
The technologies have been in development and demonstration by Gamle Mursten for eleven years. The REBRICK project created an initial market launch, which helped create a shift in technology for the management and reuse of demolition waste in Europe. Cooperation with partners in the EU’s Eco-Innovation initiative helped disseminate results, which facilitated further market growth and technological diffusion throughout the EU.
Further deployment
The project demonstrated that the technology worked in the expected area of use. The technology is now in its final form, ready for full-scale commercial distribution. Hence, it can be estimated to have reached 9 on the TRL scale.
Links:
The website