Prefabricated self-supported elements that can be used to insulate and renovate single family houses as well as multi-story buildings and decrease energy use to passive house standard.
Cost-efficient, prefabricated wall-and-roof elements can help meet the demand for more energy efficient buildings. These prefabricated elements are produced indoor and then transported to the construction area. With the in-door technique it is possible to manufactures and delivers tailored solutions to the construction industry. This contributes to benefits such as controlled production such as waste control, simplified construction process, better working climate, and in the end energy efficient houses.
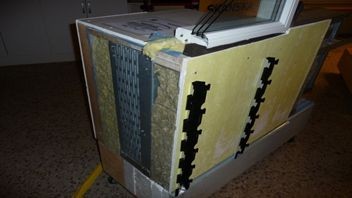
Buildings stand for approximately 40% of primary energy consumption in advanced economies[1]. Given the slow turnover of long-lived building stock, reducing energy in existing buildings will be required to meet energy and environmental targets at the national and international level. The energy performance of the existing building stock can be significantly improved by renovating and insulating houses. However, there are some complex challenges related to energy efficiency in buildings. Waste generation, environmental impact, occupational health and high costs are intricate issues which need to be solved in order to achieve a sustainable construction sector alongside an energy-efficient building stock.
The innovation
To address some of these challenges, the company Elementum Eco began to develop and produce project-tailored elements and envelope solutions for the building and construction sector. The company offers prefabricated walls and roof components featuring high quality insulation materials without organic constituents, thereby decreasing the risk of mould. The components are adjusted to customer needs to achieve the most energy-efficient building process. Sustainable manufacturing of the elements, featuring slotted steel studs and granite foam in a controlled eco-manufacturing process, improves the product life cycle and the carbon footprint. The elements are can be used in both single family houses as well as multi-storey buildings. As the elements are self-sustaining they can be used for insulation in new stories on current buildings and in that way adding more apartments to the building.
The primary layer of the wall element is on the inside, and consists of slotted steel studs to the Z-section in combination with contour-cut foam.
The outside is fire-resistant board. The result is a component that is very stable and insensitive to moisture.
The innovative insulation production utilities are modern and flexible with less material and energy use this lead to waste reductions in the construction field lowers occupational health risks by simplifying the montage, need of less material which reduces environmental impact from construction material, decreases renovation costs and makes the tailored renovation process more efficient. The building elements are commercially attractive since the offer decrease lifetime energy use during to the level of a passive house/zero emission building.
Why did it work?
Pre-fabricating walls for building construction is a well-known technology that started in the early 1600s. Since then, pre-fabricated body elements in concrete as well as wood walls and completely pre-fabricated houses have been developed. The Elmentum Ecos walls were developed during the year 2000 and were part of a pilot project in Sweden in 2006, where the residential building Brogården was renovated to a multi-story passive house. . Firstly, the walls were developed for the pilot house, with tests performed to make sure that the walls could meet passive house standards, and then changes were made to manage the passive house requirement for all the buildings in the construction project Brogården. The walls are built in a rationalized production process, with fewer layers providing the same insulation capacity, fewer screws, less waste, and much faster mounting.
Further development
The company is now entering an expansion phase with a focus on market and business development. Also the implementation of a new national production facility will help scale up this passive house technology application, which already reaches beyond 9 on the TRL scale.
VIsit the website