RFID technology improves the forestry value chain
Using RFID technology to keep track of different characteristics of incoming logs in sawmills will reduce the amount of processing waste and reduce workload. As raw material is a big share of operating costs of sawmills, the new RFID system can help improve process efficiency.
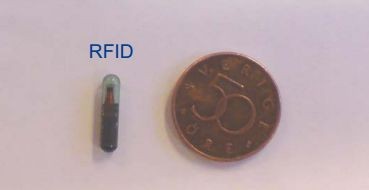
The challenge
Sawmills today face the challenge in easily sensing what properties incoming logs have. For a sawmill, raw material comprises about 70% of total operational cost. This makes identifying the properties of individual logs, including what product it is most suited for, an important task. This can reduce the share of logs wasted by being incorrectly processed for products for which they do not meet quality standards.
The innovation
To make it easier for sawmills to buy the right raw materials, a project at Munksund sawmill in Sweden implemented a tracking system that tracks where the forest specific boards and logs originate from. Munksund sawmill is owned by SCA Timber (Sweden) and the project was coordinated by Luleå University of Technology and SP Technical Research institute of Sweden. The project was financed through Träcentrum Norr, which is an association of the forestry and timber industry. In total the project had a private grant funding for R&D of 7.5 million SEK (€817 000).
To create a sustainable timber supply chain the method used for tracking logs was Radio Frequency Identification (RFID). RFID is a technology to read information remotely by applying transponders (called tags) to the logs. For the project, RFID was considered the most suitable method as it is completely insensitive to bark and other contaminants found in timber processing. A currently common application of RFID is as theft protection in clothing stores.
Each RFID tag is unique and after marking logs, an antenna can be used to read RFID tags. After the RFID tag has been read, 3D and X-ray detector systems collect and store data on the quality and possible applications of the log.
At Munksund sawmill, marking is done for batches of 400 logs. To compensate for variation within the batch, the sawmill uses a simulation program based on algorithms.
The system helps improve the process as second-class timber can be eliminated, waste reduction in terms of decreasing the amount of timber swan, workload, and in addition, allowing for production planning to be started earlier. The process is further improved as customer orders can be matched with purchases of raw material.
Why did it work?
The background to the project of the RFID on Munksund sawmill was the desire to develop, implement and evaluate an automatic test sawing system to track a subset of the incoming raw material. Testing the system in a real working environment has proven to be a success factor. Through collaboration between Luleå University of Technology and SP, the project had access to essential knowledge and expertise.
Further deployment
The project has demonstrated an integrated prototype, and is therefore estimated to be 7 on the TRL scale. There is still need for further studies to analyze the process and improve its commercial viability.