Smart delivery of cost efficient hydrogen - SPERA
Chiyoda Corporation, an engineering company in Japan, proposed the global hydrogen supply chain concept by liquid organic hydrogen carrier with Toluene /Methylcyclohexane system. In this method, hydrogen is fixed to toluene with the hydrogenation reaction and converted into SPERA Hydrogen, which can be transported by chemical tanker at the normal atmospheric temperature.
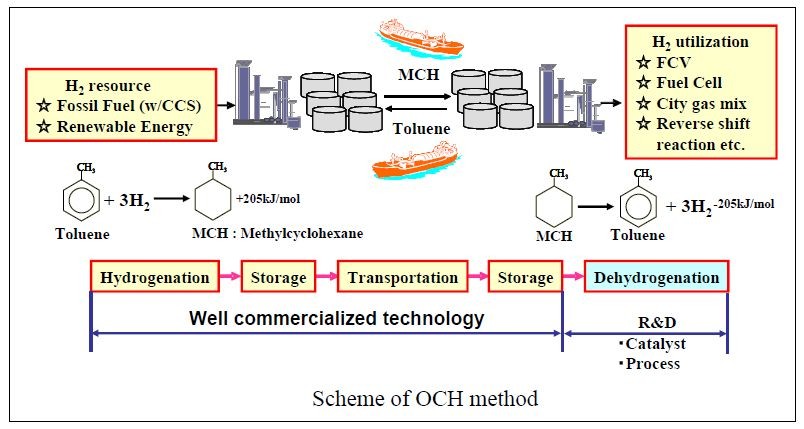
The challenge
The issues of CO2 emission and future fossil energy shortage are critical in Japan. Since Fukushima nuclear power plant accident in 2011, the importance of renewable energy usage has been emphasized in the country, for there isn’t much natural resource for producing energy domestically. The future of any country depends on a clean, sustainable energy supply. Hydrogen has the potential characteristics to provide safe, clean and affordable energy from various available resources. It is a clean energy carrier and the lightest gas, but difficult to store or transport under normal conditions. It is considered that hydrogen energy can be converted from water and renewable energy including solar energy in the future.
The innovation
Two brand-new technologies made SPERA Hydrogen possible.
1.Organic Chemical Hydride (OCH) Technology
This technology enables the transport of hydrogen at ambient temperature and pressure: fixing hydrogen to toluene, a major component of gasoline, produces a liquid called methylcyclohexane (MCH), which is suitable for use at ambient temperature and pressure. Such produced hydrogen is named SPERA Hydrogen. The structural storage of hydrogen in bulk and long-distance transportation at less cost is facilitated because it eliminates the need for hydrogen to be liquefied at cryogenic temperatures or pressurized in cylinders.
2. Dehydrogenation Catalyst
This process extracts hydrogen from MCH through a nano separating technology. So far it was considered impossible to separate hydrogen from MCH via a chemical separating process; a catalyst with proprietary nanotechnology made it. The first dehydrogenation catalyst, which Chiyoda Corporation succeeded in developing in 2004, is useful for supplying the exact amount of hydrogen on demand at any time and any place. SPERA Catalyst not only makes it possible to easily extract hydrogen from SPERA Hydrogen (MCH), but has also a long lifespan and can be mass-produced.
Why did it work?
SPERA Hydrogen has the promising potential to revolutionise the energy generation in a more sustainable economy. The next development steps are the following:
To build a hydrogenation plant to chemically fix hydrogen to toluene. Hydrogen is generated in mass quantities as a by-product of natural gas and coal production overseas. The plant liquefies the hydrogen into MCH. In the process of such chemical reaction, CO2 is generated since the site carries gas and coal. Carbon Capture and Storage (CCS) system will work on-site thereby minimising the CO2 emissions of the process.SPERA Hydrogen uses existing infrastructure such as chemical tankers and reserve tanks for its transportation and storage, thus minimising the cost of building new facilities.3. To produce hydrogen by means of water electrolysis, using electricity generated by renewable energy sources such as wind and solar power.
4. Large-scale dehydrogenation plants will be installed wherever much hydrogen is consumed, small dehydrogenation systems wherever less is consumed. Moreover, the toluene once used to transport hydrogen can be used repeatedly, enhancing further the economics of the technology.
Further deployment
After successfully setting up a demonstration plant in Yokohama, Japan in 2013, the development demonstrated its potential for improved energy efficiency in industry. The system is now in the commercial step. SPERA Hydrogen can be put to a variety of uses including power plant, automobile fuels, home fuels, stockpiles, etc. In the foreseeable future, it will be produced from natural energy resources. Not only does it avoid CO2 emissions, but it can be produced almost anywhere. The maturity of Chiyoda’s practices is estimated to be 9 on TRL scale.
The website